Are you tired of spending money on expensive clothing and accessories? Do you want to personalize your wardrobe with unique designs and patterns? Look no further than DTF transfers! These heat transfers are a popular method for creating custom apparel, allowing individuals to transfer their own designs onto fabric.

Direct to Film (DTF) transfers are revolutionizing the custom apparel industry, providing a versatile and efficient method for applying vibrant, high-quality graphics to a variety of fabrics.
This innovative technique involves printing a design onto a special film, which is then transferred onto the fabric using heat and pressure. Whether you’re a professional looking to streamline your production process or a hobbyist eager to create custom garments at home, mastering the application of DTF transfers can unlock endless creative possibilities.
This guide will walk you through the step-by-step process of how to apply DTF transfers, ensuring you achieve professional-grade results every time.
What are the Benefits of DTF Transfers?
DTF transfers offer several advantages over traditional heat transfer methods, such as screen printing or direct-to-garment (DTG) printing.
- Cost-Effective: When compared to other custom apparel techniques, DTF transfers are a cost-effective option for both small and large-scale production. Unlike screen printing, which requires the creation of individual screens for each color in a design, DTF transfers only require one film for the entire design. This significantly reduces production costs, making it an attractive option for businesses and individuals alike.
- Versatile: DTF transfers can be applied to a wide range of fabrics, including cotton, polyester, nylon, and more. This versatility makes it ideal for creating custom apparel items such as t-shirts, sweatshirts, hats, and even bags.
- High-Quality Results: With DTF transfers, designs are printed onto a thin, flexible film that adheres seamlessly to the fabric. This creates a smooth and vibrant finish that is both durable and long-lasting. Plus, since the design is transferred using heat and pressure, it becomes an integral part of the fabric, ensuring it won’t fade or crack over time.
- Easy to Use: DTF transfers are easy to use, making them accessible to individuals of all skill levels. With a little bit of practice and the right equipment, you can quickly become proficient in applying DTF transfers to various fabrics.
These are just a few of the many benefits that DTF transfers offer. Now let’s dive into the step-by-step process of how to apply them.
What Will You Need?
Before you begin, make sure you have all the necessary materials and equipment for applying DTF transfers. Here’s a list of what you’ll need:

- DTF Printer: This specialized printer is designed to adhere ink to the transfer film.
- DTF Ink: The type of ink used for DTF transfers can vary depending on the fabric being used. Make sure to use the appropriate ink for your chosen fabric.
- DTF Transfer Film: This is a thin, transparent film that acts as the carrier for the design.
- Heat Press Machine: A heat press machine will be used to transfer the design from the film onto the fabric. Make sure it can reach temperatures between 300-350°F and has adjustable pressure settings.
- Fabric: Choose the fabric you want to transfer your design onto. Make sure it is clean and free of any loose fibers or wrinkles.
- Teflon Sheet: This sheet will protect your design from direct contact with the heat press machine, preventing any potential damage.
- Scissors: You’ll need scissors to cut out the design from the film. Make sure they are sharp and precise for a clean cut.
- Tweezers: Tweezers will come in handy for removing any small pieces of film or debris that may be left behind after cutting out the design.
- Lint Roller: This will help ensure your fabric is free of any lint or stray fibers that could affect the transfer process.
Now that you have ready all your materials and equipment, it’s time to start transferring your design onto fabric!
9 Easy Steps on How to Apply Dtf Transfers
Step 1. Design Your Transfer:

The first and arguably most critical step in applying DTF transfers is to design your transfer. This is where your creativity comes into play. Utilizing graphic design software, you can either create a new design from scratch or modify an existing image to suit your project. When designing, keep in mind the dimensions of the garment or fabric onto which you’ll be transferring the design, as well as how the colors and details will appear on the specific material.
For high-quality results, ensure your design is at a high resolution (at least 300 DPI) to prevent pixelation when printed. Once satisfied with your design, mirror the image before printing. This reversal is crucial because the design will be flipped during the transfer process, ensuring it appears correctly oriented on the fabric.
Step 2. Print Your Design:
After finalizing and mirroring your design, it’s time to print it onto the DTF transfer film using your DTF printer. Ensure that your printer is loaded with the correct type of DTF ink suitable for your fabric. Feed the DTF transfer film into the printer with the matte side facing up, as this is where the ink will adhere.
Depending on your printer’s settings, you may need to adjust the color intensity or other parameters to get the best results. Once set up, print your design and give it a moment to dry completely before moving on to the next step. This careful attention to detail in the printing process is vital for achieving vibrant and crisp transfers.
Step 3. Apply Powder and Cure the Design:
Once your design has been printed on the DTF transfer film, the next step is to apply a polyurethane adhesive powder over the printed side. This powder is crucial as it serves to bind the ink to your fabric during the heat press process. Evenly sprinkle the adhesive powder across the entire design, ensuring every part of the ink is covered. After applying the powder, shake off any excess and proceed to cure the design.
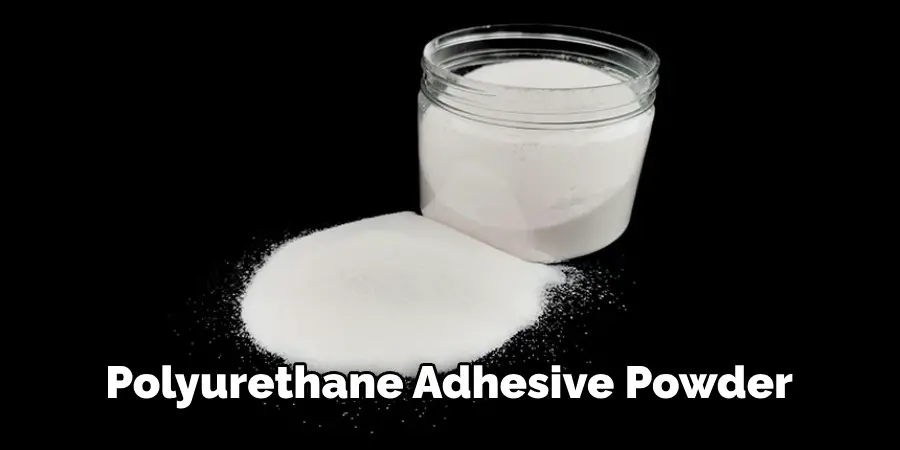
Curing can be done using a curing oven or a heat press set to a low temperature. The goal is to melt the powder without damaging the film, typically at a temperature range between 210-230°F (100-110°C) for about 2-3 minutes. This process solidifies the powder, creating a strong adhesive that will bond the design to the fabric effectively.
Step 4. Preparing Your Fabric:
Before transferring the design, it’s important to prepare the fabric to ensure the best results. Start by preheating your heat press machine to the recommended temperature for DTF transfers, usually between 300-350°F (149-177°C). Then, place your fabric on the heat press bed, ensuring it is smooth and wrinkle-free. Use the lint roller to remove any dust, lint, or stray fibers from the fabric’s surface.
This step is crucial as even a small piece of lint can cause imperfections in the transferred design. If necessary, use the heat press to pre-press the fabric for a few seconds. This will remove any moisture and further ensure a smooth surface, creating an optimal foundation for the DTF transfer.
Step 5. Position Your Design:
After preparing your fabric, the next step involves positioning your design correctly. Carefully peel the printed design off the DTF transfer film, making sure not to tear or distort it. Align the design on the fabric where you want it to be transferred.

Pay close attention to its placement, orientation, and angle to ensure it mirrors your original design plan accurately. If you’re working with clothing, consider the typical standards for positioning, such as centering the design on a shirt front or aligning it with specific garment features.
Step 6. Heat Press the Design:
Once your design is meticulously positioned on the fabric, cover it with a Teflon sheet to protect both the fabric and the transfer. Next, place the fabric in the heat press machine, ensuring the design is facing up. Clamp down the heat press firmly to apply the necessary pressure and heat. The typical pressing time is between 15 to 20 seconds, but this may vary depending on the fabric and the heat press machine’s specifications.
Make sure to follow the recommended settings for optimal results. Once the time is up, release the heat press and carefully remove the fabric. Allow the design to cool slightly before moving on to the next step.
Step 7. Peel Off the Transfer Film:
After allowing the design to cool for a few moments, carefully start peeling off the transfer film from the fabric. Do this slowly and gently to ensure the design has completely adhered to the fabric and to prevent any parts of the design from lifting off with the film.
It’s recommended to peel at a 45-degree angle for best results. If any part of the design does not seem fully transferred, you can cover it again with the Teflon sheet and re-press it for a few more seconds. Once the film is completely removed, your design should be vividly and securely transferred onto the fabric.
Step 8. Finishing Touches:
The final step in the DTF transfer process is to apply the finishing touches to ensure your design is fully set and durable. To do this, place the fabric back under the heat press, covered with a Teflon sheet, for an additional 10-15 seconds. This post-pressing step helps to solidify the bond between the design and the fabric, ensuring it will withstand washing and wearing.

After post-pressing, allow the fabric to cool down completely before handling. Scrutinize your work to make sure every part of the design is perfectly adhered to. Congratulations! You’ve completed the DTF transfer process, and your custom-designed fabric is ready to be showcased or worn proudly.
Step 9. Care and Maintenance:
To ensure the longevity of your DTF-transferred design, proper care and maintenance are essential. Always turn the fabric inside out before washing to protect the design. Use cold water and a mild detergent, avoiding bleach to prevent fading and deterioration of the adhesive.
It’s recommended to wash the fabric on a gentle cycle and to air dry it, instead of using a tumble dryer which can cause the design to crack or peel. Ironing should be done on the reverse side of the fabric to avoid direct heat on the transferred design. Following these simple care instructions will help maintain the quality and vibrancy of your DTF-transferred design for a long time.
By following these steps and tips, you can achieve professional-quality DTF transfers right in your own home or business.
5 Additional Tips and Tricks
- Use the Correct Press Settings: Getting the temperature and pressure right is crucial for a successful DTG transfer. Make sure you use the correct settings for each type of fabric and ink.
- Pre-Treat Your Garments: Pre-treating your garments before applying the transfer will help ensure that the ink adheres properly to the fabric. This is especially important for dark or colored fabrics, as the pre-treatment will create a barrier between the ink and the fabric, preventing any bleeding or fading.
- Experiment with Different Transfers: Don’t be afraid to try out different types of DTG transfers to see what works best for your designs and materials. There are various options available such as plastisol, water-based, and sublimation transfers, each with its own unique qualities.
- Test Your Transfers on Scrap Fabric: Before applying the transfer to your final garment, it’s always a good idea to test it out on a piece of scrap fabric first. This will give you an idea of how the transfer will look and adhere to your chosen material.
- Washability: Make sure to use quality DTG transfers that are designed to withstand multiple washes without fading or cracking. It’s also important to follow proper washing instructions for maintaining the longevity of your transferred designs.

With these additional tips and tricks, you can ensure that your DTG transfers come out perfectly every time.
5 Things You Should Avoid When Applying for DTF Transfers
- Skipping the Fabric Preheat: Always preheat your fabric before applying the DTF transfer. This step removes moisture and wrinkles, ensuring a smoother application process. Skipping it can lead to poor adhesion and uneven transfer.
- Ignoring Fabric Compatibility: Not all fabrics are suitable for DTF transfers. Using the wrong type of fabric can result in transfers that peel off, crack, or fade prematurely. Be sure to check the compatibility of your fabric with DTF transfers before proceeding.
- Applying Too Much Pressure: While adequate pressure is crucial for transfer adherence, too much pressure can squeeze out the ink, causing the design to blur or distort. It’s critical to find the right balance for each type of fabric and transfer paper.
- Overlooking Transfer Time: Every DTF transfer has an optimal time for application. Too short, and the transfer won’t stick well; too long, and you risk burning the fabric or yellowing the transfer. Always follow the recommended time for the best results.
- Neglecting Post-Application Care: Proper care after applying the transfer is essential for its durability. Failing to follow post-application instructions, such as curing times and washing guidelines, can drastically reduce the lifespan of your design.
- Using Low-Quality Transfers or Equipment: In addition to the above, using low-quality transfers or equipment can also negatively impact your DTF transfer results. Always invest in reputable brands and make sure to properly maintain your equipment for optimal performance.
By avoiding these common mistakes, you can ensure that your DTF transfers come out looking professional and long-lasting.
Can You Put DTF Transfers on Cotton Shirts?

Yes, DTF transfers can be applied to cotton shirts. However, it’s important to note that the end result may vary depending on the type of cotton fabric used. For example, 100% cotton will yield different results compared to a blend of cotton and polyester.
Additionally, some types of DTF transfer papers are specifically designed for use on certain fabrics, so it’s always best to check the product specifications and recommendations before starting your transfer process. This will ensure that you achieve the desired results on your cotton shirts.
Overall, DTF transfers can be a great option for cotton shirts as they offer high-quality, vibrant designs with excellent washability. Just make sure to follow the proper techniques and use compatible materials for the best outcome.
Conclusion
In conclusion, how to apply DTF transfers requires attention to detail, patience, and practice. Ensuring success involves several critical steps, including proper fabric preheating, choosing fabrics compatible with DTF technology, applying precise pressure and timing during the transfer process, and adhering to post-application care instructions.
By avoiding common pitfalls such as using low-quality materials and neglecting fabric compatibility, you can significantly improve the longevity and appearance of your designs. Remember, achieving professional and lasting results with DTF transfers is entirely possible with the right knowledge and approach.
Whether you’re a hobbyist or running a custom apparel business, the tips and precautions outlined in this guide can help you create high-quality, vibrant printwear that stands the test of time. Thank you for reaching us!
About the Author
Adrien Rowe, an expert in knitting, fiber arts, and bookbinding, promotes sustainability and creativity through workshops and tutorials. Passionate about education and community, he inspires crafters of all levels to learn, share, and grow in a supportive, idea-driven environment.
Professional Focus
Specializes in advanced knitting techniques, fiber manipulation, and textile innovation.
Expert in book arts, including cotton papermaking, handmade paper techniques, and bookbinding.
Dedicated to educating and inspiring crafters of all skill levels through tutorials, workshops, and hands-on learning experiences.
Passionate about creating a supportive community where makers can share ideas, learn, and grow.
Education History
Rhode Island School of Design (RISD) – Bachelor of Fine Arts (BFA) in Textiles.
University of Iowa Center for the Book – Master of Fine Arts (MFA) in Book Arts.
Expertise:
Advanced knitting, fiber manipulation, papermaking, bookbinding, sustainability-focused crafting, educational workshops, creative tutorials, and fostering a supportive maker community.