Crafting ceramic pipes is an ancient art form that melds functionality with artistic expression. These pipes offer a unique smoking experience, marrying the natural qualities of clay with the ritual of smoking. In this guide, we’ll explore the intricate process of making ceramic pipes, from selecting the right clay to shaping, glazing, and firing.

Whether you’re a seasoned potter looking to expand your repertoire or a novice intrigued by the idea of crafting your own smoking accessories, understanding how to make ceramic pipes opens a door to a world of creativity and craftsmanship. Join us as we delve into the techniques and considerations involved in creating these functional works of art, and discover the satisfaction of crafting a piece that not only serves a practical purpose but also reflects your unique style and personality.
The Art of Crafting Ceramic Pipes
The art of crafting ceramic pipes is a nuanced process that seamlessly blends artistic vision with functional design. It begins with the careful selection of clay, which must be pliant yet durable enough to withstand the heat of firing and, eventually, smoking.
The shaping of the clay is a meditative practice, where the artist’s hands bring form to imagination, molding the raw material into a pipe that is both aesthetically pleasing and ergonomically fitting. This stage of creation allows for immense creativity – from sleek, minimalist designs to intricate patterns and shapes inspired by nature or personal symbolism.
After shaping, the pipe undergoes a detailed glazing process, where color and texture come into play, adding another layer of uniqueness to each piece. Finally, the firing process solidifies the pipe’s form and finish, making it ready for use. Throughout each step, the maker’s connection to the material and their craft is evident, imbuing the finished pipe with a sense of personality and life that mass-produced items simply cannot replicate.
Cultural and Historical Significance

Ceramic pipes hold a prominent place in the tapestry of human history, serving not just as tools for smoking but also as cultural artifacts that provide insight into the customs, beliefs, and everyday lives of people across the world. Historically, these objects have been more than mere receptacles for tobacco or other substances; they were, and in many cultures continue to be, significant symbols of social status, spirituality, and community.
For instance, in Native American societies, ceramic pipes were often used in ceremonial contexts, intricately linked with rituals and believed to carry prayers to the spiritual world. Similarly, in various European traditions, the shape, size, and decoration of pipes could indicate the user’s social status or profession, making these items as much a statement of identity as functional tools.
The crafting methods, styles, and materials used also varied significantly across different time periods and geographies, reflecting the rich diversity of human culture and innovation. Today, the creation and use of ceramic pipes bridge past and present, enabling artisans and users alike to connect with a deep and wide-ranging heritage that spans the globe and human history.
Selecting the Right Clay for Ceramic Pipes
Choosing the correct type of clay is a fundamental step in the process of crafting ceramic pipes, as the clay’s properties will directly influence the pipe’s durability, usability, and aesthetic appeal. There are several types of clay to consider, each offering unique characteristics that can impact the final piece:

- Earthenware Clay: Recognized for its excellent plasticity, making it easy to shape and sculpt. It’s suitable for detailed work, though it’s slightly more porous after firing, which may affect the longevity and resistance to moisture if not properly glazed.
- Stoneware Clay: Lauded for its strength and durability, stoneware is a great option for pipes intended for regular use. It fires at a higher temperature, resulting in a denser and more durable material that can better withstand heat and reduce porosity.
- Porcelain Clay: Offers a fine, high-quality finish with a beautiful translucent appearance when thin. It’s the hardest type of clay, firing at the highest temperatures, providing exceptional durability. However, its delicate handling and higher firing temperatures may pose challenges for beginners.
Each type of clay has its considerations regarding workability, firing temperature, and final appearance. For example, earthenware may be an excellent place to start for those new to pottery due to its forgiving nature when being shaped. In contrast, stoneware and porcelain might appeal to more experienced potters looking for durability and a refined finish.
Ultimately, the choice of clay will depend on the artist’s skill level, the desired aesthetic, and the functional requirements of the pipe being created. Experimentation with different clays can also lead to unique discoveries and personal preferences in the crafting process.
Different Types of Clay Suitable for Pipes
While earthenware, stoneware, and porcelain are the primary types of clay used in ceramic pipe making, each category encompasses a range of specific clay bodies that can offer unique benefits and challenges to the artisan. For instance:
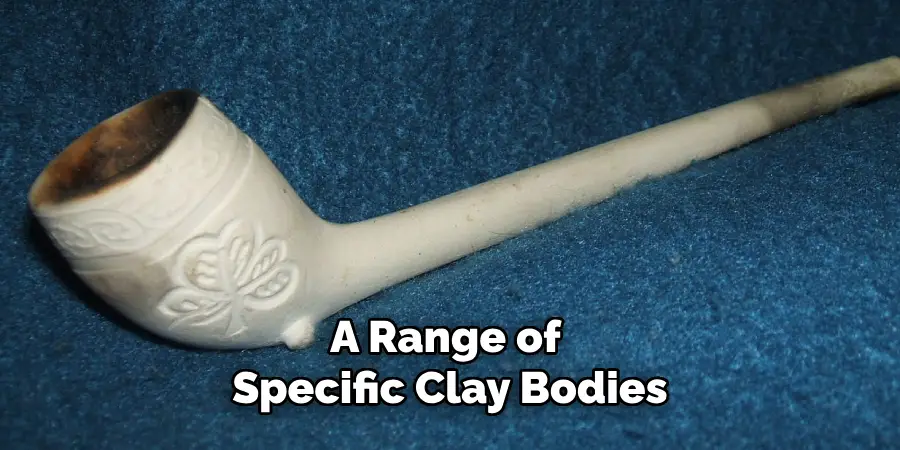
- Terracotta Clay: Often associated with earthenware, this reddish clay is highly porous and offers a rustic, organic aesthetic that can be particularly appealing for certain styles of pipes. It’s relatively easy to work with, making it a good choice for beginners, though its porosity requires a good glazing to make it more durable and suitable for smoking.
- Ball Clays: A type of earthenware clay, ball clays are highly plastic, making them excellent for forming intricate shapes. They do require a high firing temperature and thorough glazing to ensure durability and are often mixed with other clays to improve their workability and strength.
- Fireclays: Sitting between earthenware and stoneware in terms of firing temperature, fireclays are known for their ability to withstand high temperatures. This makes them an excellent choice for smoking pipes, as they can handle the heat of burning tobacco or herbs without cracking.
- Porcelain Clays: Within the porcelain category, there are variations like bone china clay, known for its high strength and whiteness, making it a luxurious option for pipes. However, its high firing temperature and brittleness when not handled correctly can be challenging for less experienced potters.
Each type of clay can be manipulated in different ways to achieve various textures, colors, and finishes, enabling artisans to create ceramic pipes that are not only functional but also reflective of personal style and artistic vision. The choice of clay will significantly influence the pipe’s final character, from a simple, earthy look with terracotta to a sophisticated, elegant finish with porcelain.
Exploring Clay Options Based on Color and Texture
When selecting clay for ceramic pipes, color and texture play as crucial a role as the material’s durability and workability. The natural color of the clay, which can range from white and light gray to deep reds and browns, significantly impacts the aesthetic of the finished pipe. For example, terracotta offers warm, earthy tones that bring a traditional vibe, while porcelain can achieve a sleek, white finish that appeals to those seeking a more modern look.

Texture is another vital consideration. Some clays, like certain stoneware clays, can be textured to add grip or decorative elements to the pipe. Other clays, particularly porcelain, lend themselves to a smooth, polished finish that feels luxurious in hand. Additionally, the clay’s inherent texture can influence the final surface; for instance, grogged clays that contain small particles of fired clay can create a rustic, tactile feel that enhances the smoking experience.
Artisans often experiment with blending clays to achieve the perfect balance of color, texture, and performance. For example, mixing stoneware and earthenware can combine the durability of stoneware with the warm colors and easy workability of earthenware. Similarly, adding small amounts of colored clays or stains to a white porcelain base can introduce subtle color variations, allowing for a custom palette that can make each pipe genuinely unique.
Gathering Tools and Materials
Before beginning the process of crafting a ceramic pipe, acquiring the right set of tools and materials is essential. This preparation ensures that the creative process proceeds smoothly from start to finish. The fundamental toolkit for working with clay includes:
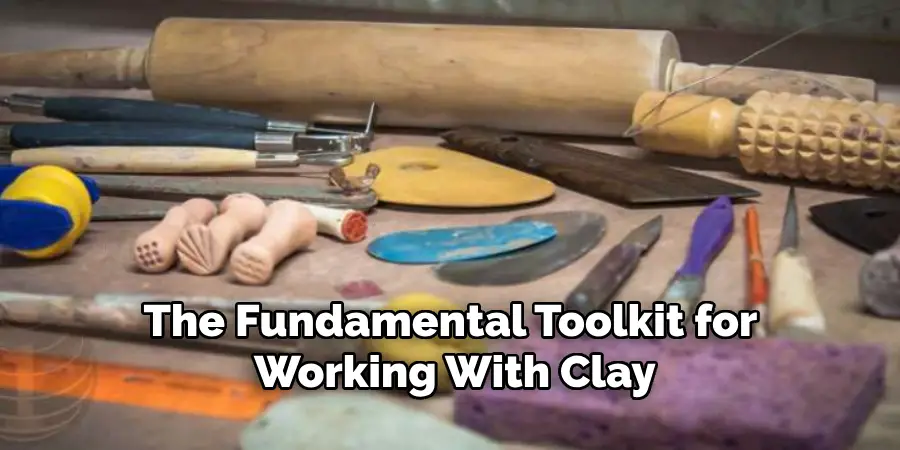
- Rolling Pin or Slab Roller: For flattening the clay to an even thickness before shaping.
- Rib Tools: Made of rubber, metal, or wood, these are used for shaping, smoothing, and compressing clay surfaces.
- Wire Clay Cutter: Essential for cutting large blocks of clay and removing finished pieces from the work surface.
- Loop and Ribbon Tools: Ideal for trimming, carving, and hollowing out clay, crucial for creating the bowl and stem of the pipe.
- Needle Tools: For cutting small intricate shapes and making holes, such as the mouthpiece and carburetor of the pipe.
- Sponges and Brushes: Used for wet smoothing of the clay and for applying glazes.
- Kiln: For firing the clay, transforming it from a soft, workable material into a hard, durable ceramic. A range of kilns, from electric to gas-powered, is suitable depending on the specific clay type and desired firing temperature.
- Glazes: These provide both aesthetic and functional benefits to the finished pipe, from vibrant colors to a protective layer that makes the piece more durable and less porous.
Essential Tools for Crafting Ceramic Pipes
Crafting ceramic pipes is a meticulous process that combines artistry with precision. Beyond the fundamental tools mentioned, there are several essential instruments that every ceramic pipe maker should have in their toolkit. These include:
- Texture Mats or Stamps: For adding unique patterns or designs to the clay, giving each pipe a distinct look and feel.
- Fettling Knives: Useful for cutting and refining the shape of the clay, these knives allow for precise adjustments to the form of the pipe.
- Calipers: To measure the dimensions of the pipe accurately, ensuring that each part fits together perfectly.
- Work Surface: A non-stick surface such as a silicone mat or a large, smooth tile is crucial for rolling out and working with clay without it sticking or picking up unwanted textures.
- Detailing Tools: Small, pointed tools for adding fine details or for carving intricate designs into the clay body of the pipe. These can range from commercially available modeling tools to homemade instruments fashioned from materials like bamboo or metal.
- Molds: For those looking to produce multiple pipes of the same shape and size, plaster or silicone molds can be used to cast the clay efficiently.
- Drying Racks or Boards: Proper drying is crucial to prevent warping or cracking. Racks or boards provide an even air flow around the pieces, allowing them to dry uniformly.
- Glaze Mixing Tools: If custom glazes are used, tools for mixing and applying these glazes, such as sieves, mixers, and measuring devices, are necessary for achieving consistent and safe results.
- Safety Gear: Due to the dust and chemicals involved in crafting ceramic pipes, protective gear such as respirators, safety glasses, and dust masks are critical for health and safety in the studio.
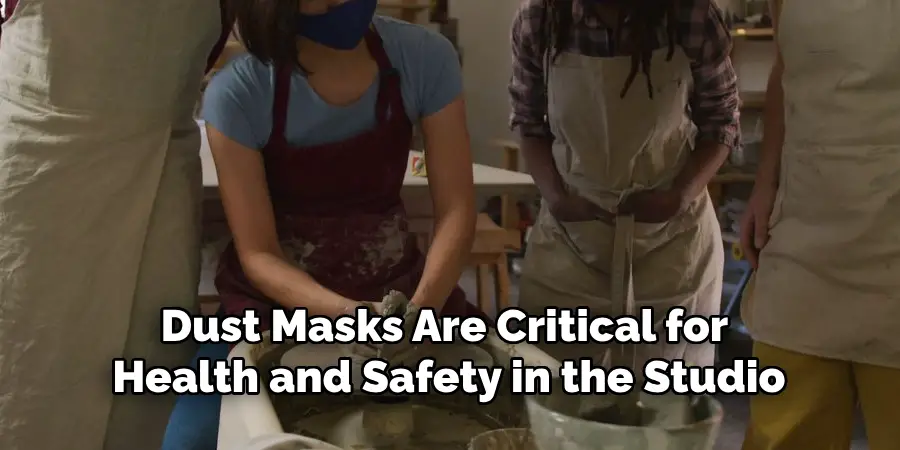
10 Methods How to Make Ceramic Pipes
1.Understanding Ceramic Pipes:
Begin by understanding the appeal and functionality of ceramic pipes in smoking culture. Ceramic pipes offer durability, heat resistance, and customization options that appeal to smokers and collectors alike. Explore the different types of ceramic pipes, including chillums, spoons, and Sherlock-style pipes, to understand their unique characteristics and designs.
2.Gathering Materials and Tools:
Before diving into pipe-making, gather the necessary materials and tools. You’ll need clay suitable for pipe-making, glazes for decoration, and essential tools such as a pottery wheel, carving tools, and a kiln. Choose the type of clay that best suits your design preferences and ensure you have all the necessary equipment to start crafting.
3.Designing and Shaping the Pipes:
Start the creative process by sketching pipe designs on paper. Consider factors such as shape, size, and functionality when designing your pipes. Use a pottery wheel or hand-building techniques to shape the clay into pipe forms, ensuring smooth surfaces and proper proportions. Experiment with different design elements and details to create unique and visually appealing pipes.
4.Carving and Sculpting:
Once the basic shape of the pipe is formed, it’s time to refine the details through carving and sculpting. Use carving tools to hollow out bowl chambers, carve airflow channels, and shape the mouthpiece. Sculpt additional features such as decorative patterns, textures, or figurative elements to enhance the aesthetic appeal of the pipes. Take your time and pay attention to detail to achieve the desired look and functionality.
5.Drying and Firing Process:
Properly drying and firing the pipes is essential to ensure their strength and durability. Allow the pipes to dry slowly and evenly to prevent cracking or warping. Once dry, bisque fire the pipes in a kiln to strengthen the clay and prepare it for glazing. Follow the recommended firing schedule and temperature to achieve the desired results.
6.Glazing and Decorating:
Get creative with glazing and decorating your ceramic pipes to add color and personality. Experiment with different glaze colors, finishes, and techniques to achieve unique effects. Apply glazes evenly to the pipes using brushes or dipping methods, taking care to cover the entire surface. Explore decorative techniques such as wax resist, sgraffito, or layering to create intricate designs and patterns.
7.Firing and Final Touches:
Once the pipes are glazed and decorated, it’s time for the final firing. Load the pipes into the kiln carefully, ensuring they are spaced apart to allow for even heat distribution. Fire the pipes to the appropriate temperature for the type of clay and glazes used, following the recommended firing schedule. After firing, inspect the pipes for any imperfections and make any necessary final touches, such as sanding or polishing, to ensure a smooth finish.
8.Safety Precautions and Best Practices:
Prioritize safety when working with clay, glazes, and kilns to protect yourself and others from potential hazards. Ensure proper ventilation in your workspace and use protective equipment such as gloves and goggles when handling materials. Follow best practices for cleaning equipment and maintaining a safe working environment to prevent accidents and injuries.
9.Caring for Ceramic Pipes:
Educate users on how to care for ceramic pipes to prolong their lifespan and maintain their quality. Provide instructions for cleaning the pipes regularly to remove resin buildup and prevent clogs in the airflow channels. Advise users to store the pipes safely when not in use and protect them from damage or breakage.

10.Customization and Personalization:
Encourage creativity and personalization by offering custom options for ceramic pipes. Allow customers to choose from a variety of designs, colors, and finishes to create a pipe that reflects their unique style and preferences. Consider offering custom engraving or personalization services to add an extra touch of individuality to each pipe.
Conclusion
In conclusion, the process of making ceramic pipes is a fusion of skill, creativity, and tradition, offering a deeply satisfying journey for both experienced potters and beginners alike. Through this guide, we’ve explored the intricate steps involved in crafting these functional yet aesthetically pleasing smoking accessories, from clay selection to shaping, glazing, and firing.
As you embark on your own ceramic pipe-making endeavors, remember to embrace experimentation, learn from each piece you create, and let your creativity flourish. Be sure to follow all instructions on how to make ceramic pipes carefully, and always consult an expert when in doubt.
About the Author
Adrien Rowe, an expert in knitting, fiber arts, and bookbinding, promotes sustainability and creativity through workshops and tutorials. Passionate about education and community, he inspires crafters of all levels to learn, share, and grow in a supportive, idea-driven environment.
Professional Focus
Specializes in advanced knitting techniques, fiber manipulation, and textile innovation.
Expert in book arts, including cotton papermaking, handmade paper techniques, and bookbinding.
Dedicated to educating and inspiring crafters of all skill levels through tutorials, workshops, and hands-on learning experiences.
Passionate about creating a supportive community where makers can share ideas, learn, and grow.
Education History
Rhode Island School of Design (RISD) – Bachelor of Fine Arts (BFA) in Textiles.
University of Iowa Center for the Book – Master of Fine Arts (MFA) in Book Arts.
Expertise:
Advanced knitting, fiber manipulation, papermaking, bookbinding, sustainability-focused crafting, educational workshops, creative tutorials, and fostering a supportive maker community.