Creating a slip casting mold opens up a world of possibilities for ceramic artists, allowing them to replicate intricate shapes and designs with precision and consistency. Whether you’re a beginner looking to delve into the art of slip casting or an experienced potter seeking to expand your repertoire, mastering the process of making molds is essential.

From sculptural forms to functional objects, slip casting molds offer endless potential for creativity and experimentation. The process involves creating a negative impression of the desired object, which is then used to cast multiple replicas using liquid clay (slip).
In this comprehensive guide, we’ll explore the step-by-step process of how to make a slip casting mold, covering essential techniques, materials, and tips to help you achieve success. Whether you’re creating molds for personal projects or production purposes, this guide will equip you with the knowledge and confidence to create high-quality molds that elevate your ceramic creations to new heights.
Importance of Slip Casting Molds in Ceramics
Slip casting molds play a pivotal role in the world of ceramics, offering artists the ability to produce precise, uniform pieces that would be exceedingly difficult, if not impossible, to replicate by hand. This method is particularly valuable for producing complex or intricate shapes, where the consistency of thickness and detail is paramount.
Furthermore, slip casting molds enable ceramists to achieve a high level of productivity, allowing for the efficient mass production of items without sacrificing quality or craftsmanship. This efficiency opens up opportunities for artists to expand their offerings, experimenting with limited editions or variations on a theme with relative ease.

Additionally, the use of molds in ceramics has democratized the production of ceramic goods, making high-quality, decorative, and functional pieces more accessible to a wider audience. Whether for creating singular artistic statements or for the practical replication of designs, slip casting molds are an indispensable tool in the ceramicist’s toolkit, bridging the gap between artisanal craftsmanship and industrial production.
Benefits of DIY Mold Making
Engaging in DIY mold making for slip casting offers artists not only a high degree of creative freedom but also a plethora of practical advantages. Firstly, it allows for complete customization, enabling ceramists to bring their unique visions to life without the constraints of commercially available molds. This bespoke approach means that almost any concept or design can be realized, providing a canvas for limitless artistic expression.
Additionally, mastering the skill of mold making empowers artists to produce work more economically. Rather than investing in expensive pre-made molds, creating your own can significantly reduce costs, especially beneficial for those producing large quantities or experimenting with multiple prototypes. Another benefit is the ability for instant iteration and adaptation.
If a design doesn’t turn out as expected, having the skill to modify molds or create new ones quickly is invaluable for the refinement process, ensuring the final products meet the artist’s exacting standards. DIY mold making fosters a deeper understanding of the materials and processes involved, enriching the artist’s craft and potentially inspiring innovative techniques and applications.
Understanding Slip Casting and Mold Making
Slip casting is a technique used in ceramics to create complex and detailed shapes that would be difficult to achieve with traditional hand-building or wheel-throwing methods.
The process involves pouring liquid clay, or slip, into a porous plaster mold; the plaster absorbs water from the slip, leaving a clay body that mirrors the mold’s inner surfaces. Once the clay reaches the desired thickness, the excess slip is poured out, and the formed clay is left to harden slightly before the mold is opened and the new clay object is carefully removed.
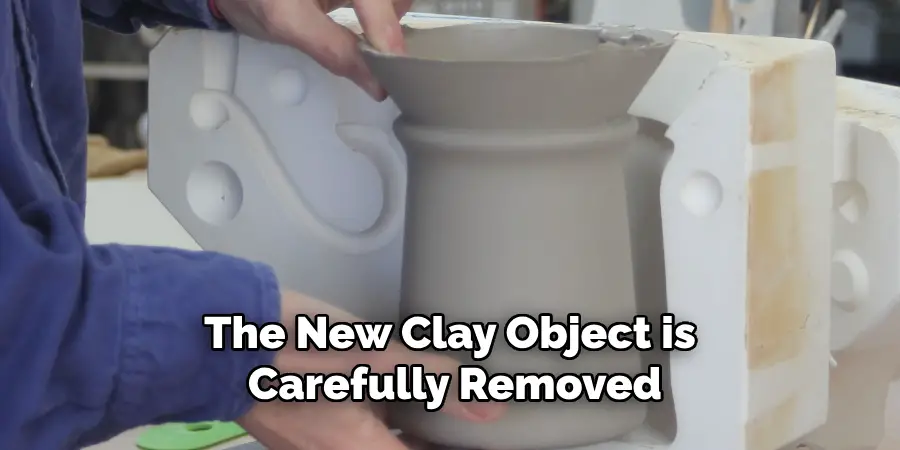
Mold making, on the other hand, is the art of creating these crucial negative spaces that will shape the slip into the ceramist’s desired forms. It often begins with a prototype of the object to be replicated, from which a plaster mold is crafted. This mold can be a simple one-piece design for flat or open objects or a more complex multi-part mold for items with undercuts or intricate details.
The key to successful mold making lies in understanding the properties of both the plaster and the slip, as well as the intricacies of the object being molded. The mold must be designed not only to accurately capture the details of the original design but also to allow for easy removal of the finished piece without damage.
This deep synergy between slip casting and mold making unlocks a realm of potential for ceramic artists, combining precision engineering with creative vision. By mastering these processes, artists can reproduce their most beloved designs with consistency or explore new forms with confidence, knowing that each piece will maintain the high quality and uniqueness of handmade art, even in series production.
Importance of Quality Molds in Slip Casting
High-quality molds are the linchpin of successful slip casting, critically influencing the outcome of the final ceramic pieces. The precision and integrity of a mold directly affect the smoothness, detail, and structural integrity of slip-cast items. Molds made from superior materials with meticulous craftsmanship can ensure even absorption of moisture from the slip, which is essential for achieving uniform wall thicknesses in the final product.
This uniformity is not just aesthetic; it also ensures that the ceramic pieces are structurally sound and functional. Furthermore, high-quality molds have a longer lifespan, allowing for the production of numerous copies without degradation of detail or accuracy. They also offer better release qualities, making demolding easier and reducing the risk of damaging delicate features.
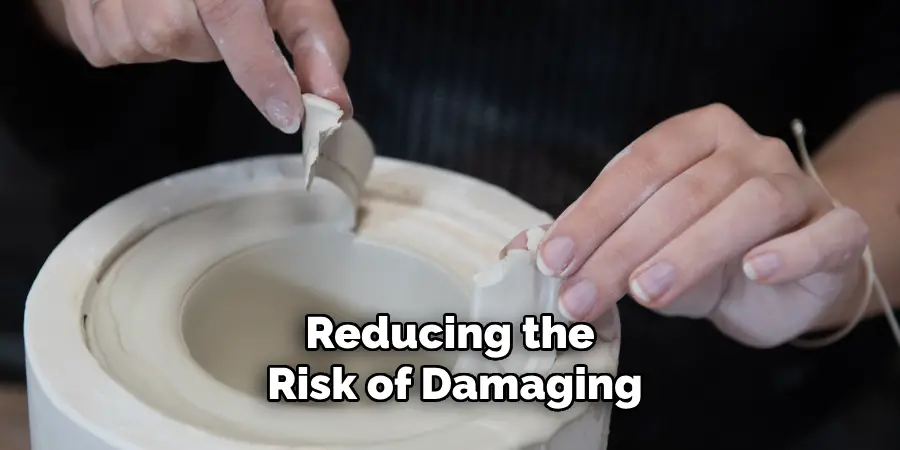
Investing in the creation or procurement of quality molds is therefore essential for ceramists looking to not only preserve the artistic integrity of their designs but also optimize their production efficiency and minimize waste. In essence, the quality of the mold sets the foundation for the quality of the final ceramic piece, underscoring the importance of excellence in mold making within the slip casting process.
Gathering Necessary Materials and Tools
Before beginning the mold-making and slip-casting process, ensuring you have all the necessary materials and tools is essential for a smooth and successful project. The foundation of mold making starts with a high-quality plaster, typically Plaster of Paris, which is known for its excellent water absorption properties and fine detail reproduction. You’ll also need clay to create the original model, along with a variety of sculpting tools to refine its shape.
For the slip casting itself, a supply of liquid slip, preferably in the desired clay body, is necessary. Tools for mixing and sieving the slip ensure a smooth, consistent texture free of impurities, which could affect the final product’s quality.
The mold making process requires additional tools and materials, including release agents such as soap or oil to ensure easy separation of the mold from the model, and cottle boards or mold straps to secure the mold while it sets. Measuring cups and mixing tools are needed for preparing the plaster, and a scale might be required to measure out components accurately.
Safety equipment is also crucial, including gloves to protect your hands from the abrasive qualities of plaster and slip, and a dust mask or respirator to avoid inhaling plaster dust during mixing and pouring. Eye protection is recommended when working with materials that can splash or create dust.
Collecting these materials and tools prior to starting your project will facilitate a more efficient and enjoyable mold-making and slip-casting experience.

Essential Supplies for Mold Making
When venturing into the realm of mold making, having the right supplies at your disposal is crucial for achieving high-quality results. Key among these supplies is high-quality plaster, such as Plaster of Paris, renowned for its excellent properties in capturing intricate details and absorbing moisture effectively. The choice of plaster is pivotal as it forms the backbone of the mold, determining not only the fineness of the details that can be captured but also the durability and longevity of the mold itself.
In addition to plaster, a quality release agent is indispensable. This could be a specially formulated mold soap, petroleum jelly, or a professional-grade release spray. The proper release agent will ensure that your original model can be separated from the mold without damage, preserving the integrity of both your model and the mold.
Modeling clay is another essential supply, used to create the initial model from which the mold is made. This clay needs to be malleable yet capable of holding fine details. Various sculpting tools are also necessary to refine the model’s shape, adding textures and details that will be transferred to the final mold.
For those creating complex molds, cottle boards or mold straps are essential for constructing and securing the mold walls during the setting process. These materials help in keeping the plaster mold enclosed and stable, preventing leaks and maintaining the desired shape until the plaster sets firmly.
Accurate measuring devices such as cups and scales are critical for mixing plaster and other components to the correct ratios, ensuring consistency and quality in every mold you produce. Lastly, personal protective equipment, including gloves, dust masks or respirators, and protective eyewear, should not be overlooked. These safety items protect you from the hazards of working with fine, potentially irritating plaster dust and other materials involved in mold making.
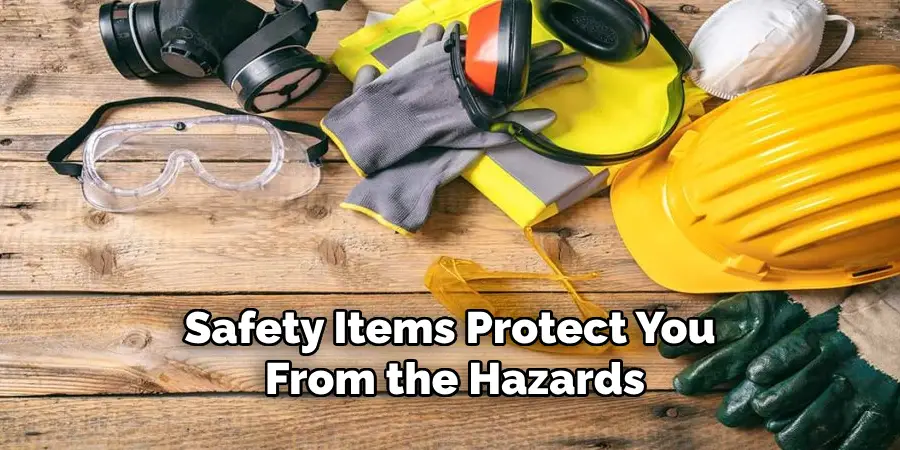
Designing the Mold Prototype
Before the actual mold-making process begins, designing a precise prototype of the desired final product is critical. This initial step involves conceptualizing the design and transferring it onto a material that can be manipulated, typically modeling clay.
The prototype serves as a physical blueprint for the mold, allowing the artist to foresee and adjust the functionality and aesthetics of the final piece. During this phase, attention to detail is paramount, as the prototype will dictate the mold’s interior contours and, consequently, the slip-cast ceramic piece’s exterior surface.
Careful consideration must also be given to the mold’s parting line, where the mold will be divided to release the cast piece. This necessitates a design that not only accounts for the artistry of the piece but also its practicality in demolding without damage. Additionally, planning for key and notch systems at this stage will ensure proper alignment of the mold halves during casting, resulting in seamless final products.
Close collaboration between the artist and the mold maker can be essential, especially for complex designs. This teamwork ensures that the prototype fulfills both the creative vision and the technical requirements for slip casting, laying a solid foundation for the subsequent steps in the mold-making process.
10 Methods How to Make a Slip Casting Mold
Method 1: Designing the Prototype
Begin by designing the prototype of the object you wish to replicate. Sketch out the shape and dimensions of the object on paper or create a 3D model using modeling clay or digital software. Ensure that the prototype is well-constructed and free of imperfections, as it will serve as the basis for your mold.
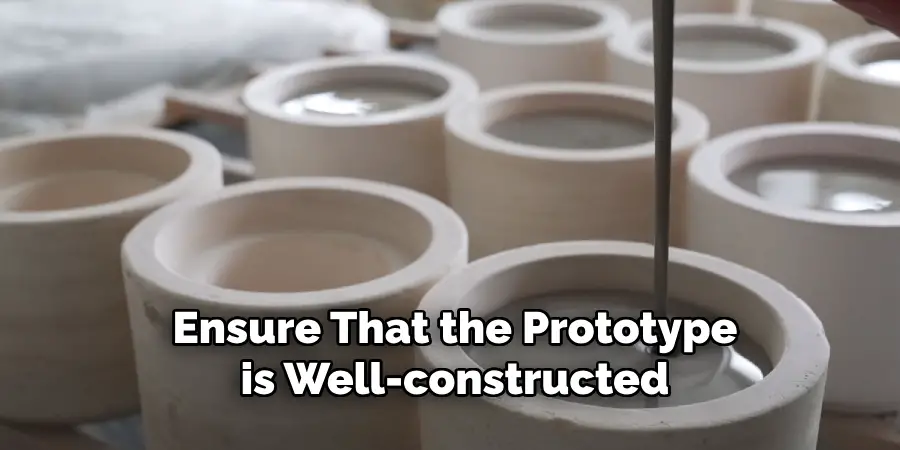
Method 2: Building the Mold Box
Construct a mold box or frame around the prototype to contain the mold material. Use materials such as wood, plastic, or foam board to create a sturdy and leak-proof enclosure. Seal the edges of the mold box with tape or clay to prevent the mold material from leaking out during pouring.
Method 3: Applying Mold Release Agent
Before pouring the mold material, apply a mold release agent to the surface of the prototype to prevent it from sticking to the mold. Use a brush or spray bottle to evenly coat the prototype with the release agent, ensuring full coverage. Allow the release agent to dry completely before proceeding. This method is particularly useful for complex or detailed prototypes that may have hard-to-reach areas.
Method 4: Mixing the Mold Material
Choose a suitable mold material for your project, such as silicone rubber, urethane rubber, or plaster. Follow the manufacturer’s instructions to mix the mold material to the correct consistency, taking care to measure the proportions accurately. Stir the mixture thoroughly to ensure uniformity.
After mixing, pour the mold material into the mold box or directly onto the object. Gently tap the mold box to release any air bubbles that may have formed. Allow the mold material to cure according to the manufacturer’s instructions. Once cured, carefully remove the mold from the mold box or object.
Method 5: Pouring the Mold Material
Carefully pour the mixed mold material into the mold box, covering the prototype completely. Pour the material slowly and steadily to minimize air bubbles and ensure even coverage. Tap the sides of the mold box gently to release any trapped air bubbles and help the mold material settle.
Method 6: Allowing the Mold to Cure
Once the mold material is poured, allow it to cure and harden according to the manufacturer’s instructions. The curing time will vary depending on the type of mold material used, so refer to the product specifications for guidance. Avoid disturbing the mold during the curing process to prevent defects.
Method 7: Demolding the Mold
After the mold has fully cured, carefully remove the mold box and demold the mold from the prototype. Gently flex the mold box to release the mold material, then carefully peel away any tape or clay sealing the edges. Take your time to avoid damaging the mold or prototype.
Method 8: Cleaning and Finishing the Mold
Inspect the mold for any imperfections or rough edges and trim away any excess material using a sharp knife or scissors. Use sandpaper or a fine-grit abrasive sponge to smooth the surface of the mold and remove any rough spots. Clean the mold thoroughly to remove any residue or debris.
Method 9: Testing the Mold
Before using the mold for casting, conduct a test to ensure that it produces satisfactory results. Mix a small batch of casting slip according to your recipe and pour it into the mold. Allow the slip to set for the recommended time, then demold the cast object and inspect it for quality and detail.
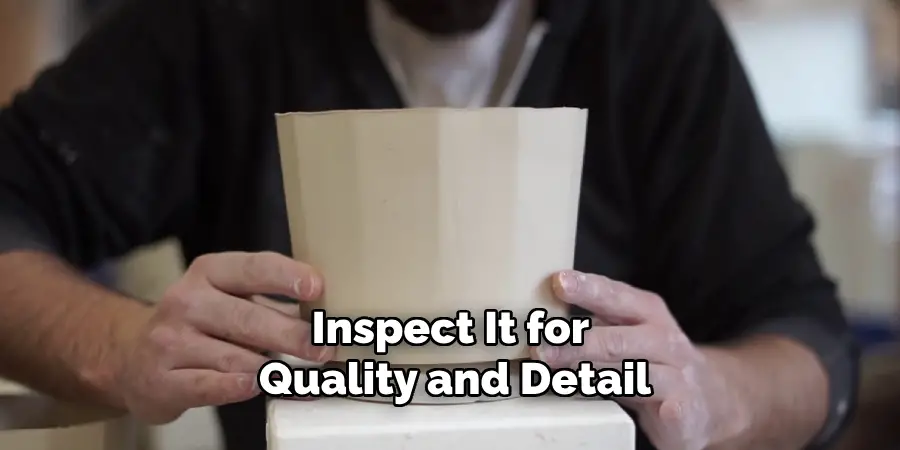
Method 10: Storing and Maintaining the Mold
Once the mold has been tested and approved, store it in a cool, dry place away from direct sunlight and moisture. Protect the mold from damage by wrapping it in bubble wrap or storing it in a sturdy container. Regularly inspect the mold for signs of wear or damage and repair as needed.
Conclusion
In conclusion, mastering the art of making slip casting molds is a valuable skill that empowers ceramic artists to create intricate and consistent forms with ease. By following the techniques outlined in this guide and experimenting with different materials and methods, you can produce molds that faithfully capture the details and nuances of your original objects.
Whether you’re casting functional pottery, sculptural pieces, or decorative objects, the versatility of slip casting molds offers endless possibilities for artistic expression. With practice and dedication, you can refine your mold-making technique and streamline your production process, allowing you to create multiples of your designs efficiently and effectively. Thanks for reading, and we hope this has given you some inspiration on how to make a slip casting mold!
About the Author
Adrien Rowe, an expert in knitting, fiber arts, and bookbinding, promotes sustainability and creativity through workshops and tutorials. Passionate about education and community, he inspires crafters of all levels to learn, share, and grow in a supportive, idea-driven environment.
Professional Focus
Specializes in advanced knitting techniques, fiber manipulation, and textile innovation.
Expert in book arts, including cotton papermaking, handmade paper techniques, and bookbinding.
Dedicated to educating and inspiring crafters of all skill levels through tutorials, workshops, and hands-on learning experiences.
Passionate about creating a supportive community where makers can share ideas, learn, and grow.
Education History
Rhode Island School of Design (RISD) – Bachelor of Fine Arts (BFA) in Textiles.
University of Iowa Center for the Book – Master of Fine Arts (MFA) in Book Arts.
Expertise:
Advanced knitting, fiber manipulation, papermaking, bookbinding, sustainability-focused crafting, educational workshops, creative tutorials, and fostering a supportive maker community.