Creating a clay house is a fun and engaging activity that combines creativity with craftsmanship. Whether you’re building a miniature model for a diorama, crafting pottery projects, or exploring full-scale adobe-style construction, making a clay house allows you to bring imaginative designs to life. This versatile project has applications in education, arts, and even sustainable architecture. The process involves selecting the right materials, shaping the structure, and adding finishing touches to achieve the desired result.
This guide on how to make a clay house will walk you through every step of the process. Perfect for hobbyists, students, or anyone interested in earthen construction, this article will provide valuable insights into the techniques and tools required to build a clay house of any size or purpose.
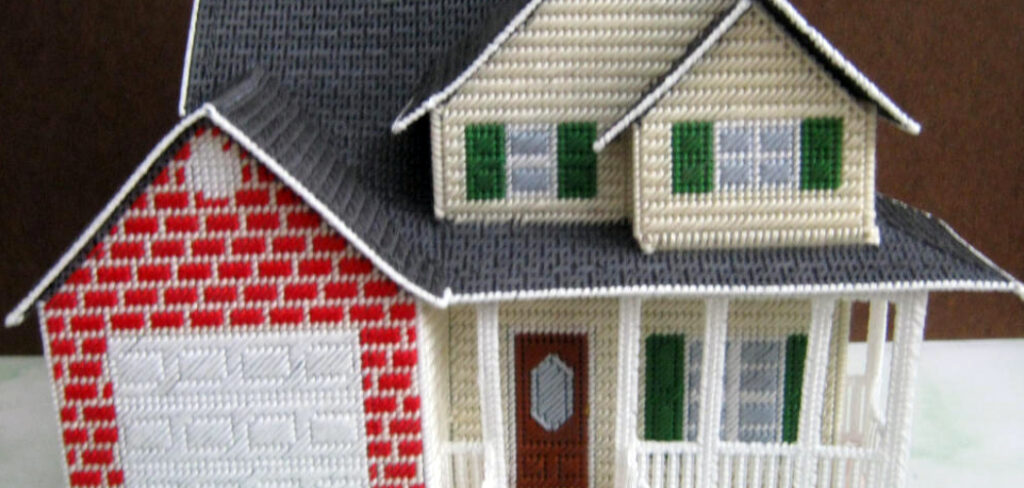
Materials and Tools Needed
Building a clay house requires selecting the right types of clay and gathering essential tools to shape and complete your project. Below is a detailed list of the materials and tools needed to get started:
Types of Clay
- Air-dry Clay: Ideal for small models and beginner projects as it doesn’t require a kiln. It’s simple to use and dries naturally over time.
- Polymer Clay: Perfect for creating detailed miniatures. This type of clay is bakeable and hardens in the oven, ensuring durability.
- Natural Clay: Best suited for larger or real-life adobe houses. It offers a traditional approach, especially when combined with sustainable construction techniques.
Additional Materials
- Sculpting Tools: Wooden or plastic tools are essential for shaping and carving the clay into intricate designs.
- Rolling Pin or Flat Surface: Used to flatten clay evenly, making it easier to construct walls and structural components.
- Water and Sponge: Necessary for smoothing the surfaces and joining clay pieces seamlessly.
- Molds or Forms: Useful for shaping walls, roofs, or other structural parts to achieve a uniform look.
- Paint, Varnish, or Sealant (optional): These finishing materials can be applied to enhance the durability and appearance of your diy clay house.
With these materials and tools in hand, you’ll be well-equipped to start creating a clay house that’s both functional and artistic.
Planning and Designing the Clay House
Sketching the House Design
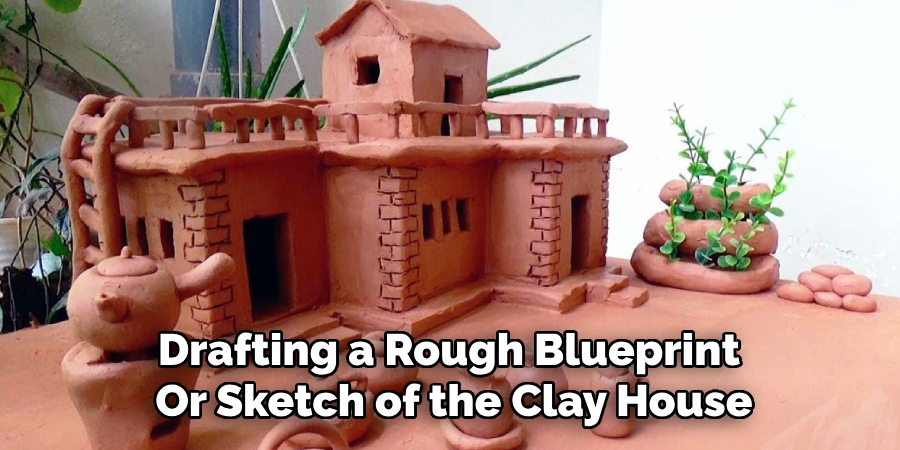
Begin your project by drafting a rough blueprint or sketch of the clay house. This step is crucial to visualize the final structure and ensure all components fit together seamlessly. Include details like the walls, roof, windows, and doors in your design. A well-thought-out plan will guide the building process and help avoid errors or missed elements.
Determining Scale and Size
Decide on the appropriate scale and size for your clay house based on its intended purpose. For instance, a compact model might suffice if you’re crafting a small decorative piece. On the other hand, consider dimensions that accommodate aesthetic appeal and utility if designing a functional item like a birdhouse. Properly determining the size ensures your clay house serves its purpose effectively.
Creating a Framework (Optional)
For larger clay houses, creating a supportive framework can enhance stability and make the building process more manageable. This can include a wireframe, cardboard base, or an armature to provide structural support. A sturdy framework can prevent sagging or collapsing during shaping and drying, resulting in a more durable and polished final product.
How to Make a Clay House: Shaping and Assembling the Clay House
Step 1: Preparing the Clay
Begin by preparing the clay to ensure it is pliable and easy to work with. Knead the clay thoroughly to soften it and eliminate any air bubbles, which could weaken the structure. Next, roll the clay into sheets of uniform thickness to create a consistent base for the house components. A rolling pin or similar tool works well for this step.
Step 2: Making the Walls
Cut out rectangular slabs of clay using a knife or a sculpting tool to form the walls. Ensure the edges are smooth and neat for easier assembly. Use a scoring technique to scratch the edges where the slabs will join lightly. Apply slip, a mixture of clay and water, along the scored edges to act as a sturdy adhesive. Carefully press the slabs together at right angles and allow them to set slightly.
Step 3: Creating Doors and Windows
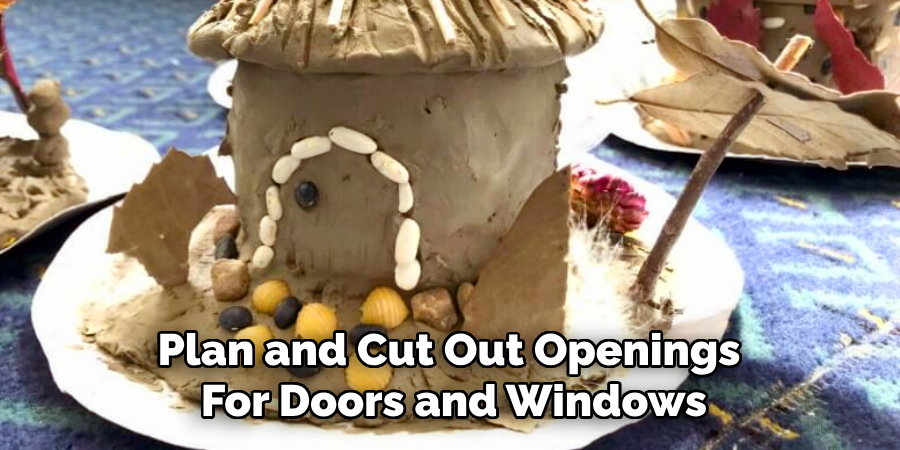
Before the clay dries, plan and cut out openings for doors and windows in the walls. Use a sharp tool to carve the shapes, ensuring precision. After cutting, smooth out any rough or sharp edges with a damp sponge to avoid cracks during drying. You can add extra details like window frames or decorative trims to enhance the design.
Step 4: Adding the Roof
Finally, shape the roof based on your desired design, whether it is flat, slanted, or thatched. Create the roof separately and attach it securely using slip if it is meant to be fixed. The roof can be left unattached as a removable piece for easy access to the interior. It should be aligned perfectly with the walls for a polished and stable finish.
Drying and Firing the Clay House
For Air-Dry Clay
Allow the clay house to air-dry naturally in a well-ventilated space for 24-48 hours. Avoid placing it in direct sunlight as this can cause the clay to dry unevenly and result in cracks. Ensure the house is placed on a flat, stable surface during drying to maintain its shape. Rotate it carefully, if necessary, to promote even drying.
For Polymer Clay
Bake the clay house in an oven following the temperature and time guidelines provided by the clay manufacturer. Typically, this involves baking at 265°F–275°F for around 15-30 minutes, depending on the size and thickness of the piece. Place the house on a baking sheet lined with parchment paper to avoid sticking. Be cautious not to overbake, as this can lead to discoloration or damage to the clay.
For Natural Clay
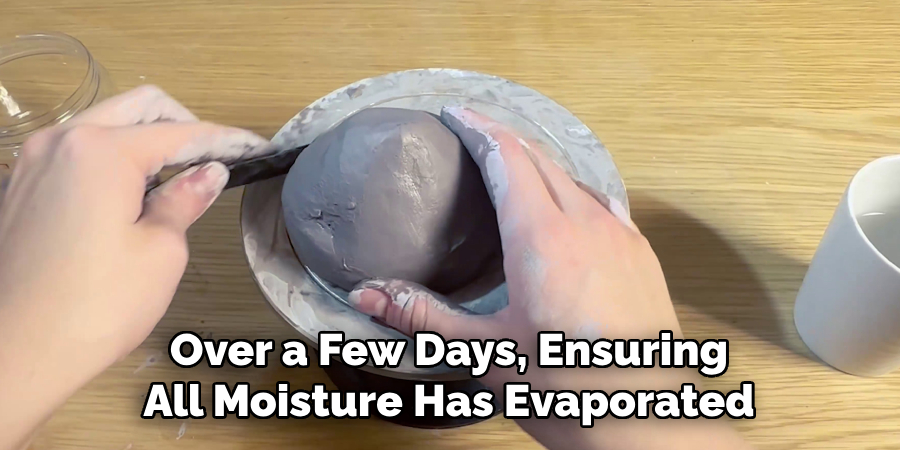
Allow the house to air-dry completely over a few days, ensuring all moisture has evaporated before moving to the firing stage. Firing the house in a kiln is essential for durability and strength, and this process usually requires temperatures between 1800°F–2300°F. Gradually increase the heat to prevent the clay from cracking under the rapid temperature change. Once fired, the clay house will have a robust, long-lasting finish suitable for decoration or functional use.
Painting and Decorating the Clay House
Once the clay house is fired and fully prepared, it’s time to add color and personality through painting and decorating.
Choosing the Right Paint
Selecting the appropriate paint is crucial for achieving the desired look and ensuring durability. Acrylic paint is excellent for bright, long-lasting colors that won’t fade over time. If you prefer a more subdued or natural appearance, consider using watercolor or clay stains to create a rustic effect that complements the clay’s texture.
Adding Textures and Details
To enhance the charm of your clay house, consider adding textures and small details. Use a toothpick or fine carving tools to etch patterns like brick or wood textures onto the surface. For added dimension, craft small clay additions such as chimneys, flower pots, or window shutters, and carefully attach them with slip or clay adhesive before painting.
Sealing for Durability
After painting and decorating, apply a clear sealant to protect the clay house from moisture and wear. A sealant prolongs the piece’s life and gives it a finished look. For a personalized touch, choose between a matte or glossy finish, depending on your preference for a subdued or polished appearance.
Troubleshooting Common Issues
Cracking Issues
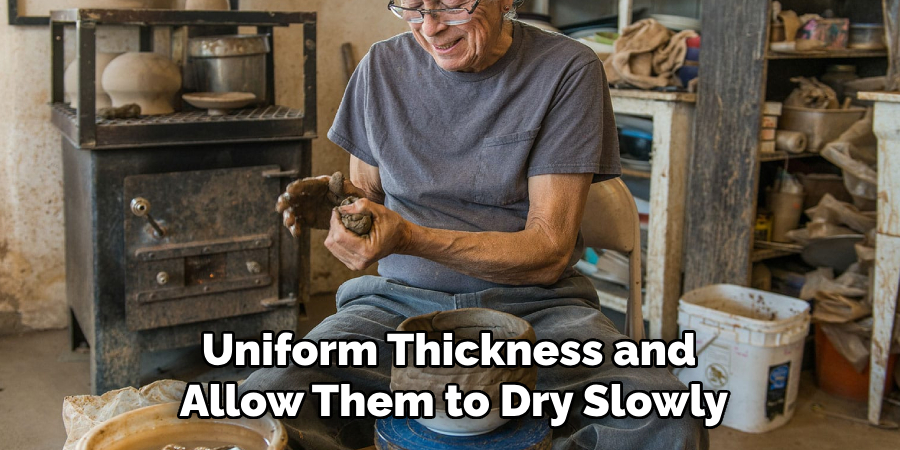
Cracking can occur if the clay dries too quickly or if your project has uneven thicknesses. To prevent this, ensure that all sections of the clay house are of a uniform thickness and allow them to dry slowly in a controlled environment. Covering the piece lightly with plastic sheeting can help regulate the drying process. For small cracks that appear before the structure is fully dry, use slip—a mixture of clay and water—to fill them in carefully. Gently smooth the area with a damp brush to blend the repair seamlessly into the surface.
Clay Not Sticking Together
When assembling different parts of your clay house, always score the surfaces where they will join. Use a sharp tool to create shallow cross-hatch marks on both pieces, then apply slip to these areas. Press the pieces together firmly but gently, ensuring there are no gaps or air pockets. This method creates a strong bond that prevents the sections from separating during drying or firing.
Roof or Walls Warping
Warping of the roof or walls is often due to uneven drying or lack of support. Dry your project flat and ensure all sides are drying similarly. To prevent large flat sections from curling or distorting, use small, lightweight objects as supports or weights during drying. This will help maintain the intended shape of your clay house.
Conclusion
Crafting a clay house is a rewarding process that combines creativity and patience. You can create a sturdy and beautifully finished piece by following the essential steps—preparing clay, shaping walls, assembling the house, drying, painting, and sealing. Remember, understanding “how to make a clay house” lies in practice and experimentation. Don’t hesitate to explore unique designs, incorporate various materials, or try new decoration techniques to personalize your creation. Take your time during each stage to ensure the best results and enjoy the satisfaction of bringing your imaginative clay house to life.
Professional Focus:
Dedicated to exploring and advancing the intersection of traditional craftsmanship and contemporary design. Specializing in textile arts, woodworking, and mixed media, with a commitment to sustainable practices and the art of upcycling. Focused on creating meaningful connections through craft, empowering individuals to unlock their creativity, and preserving cultural heritage through innovative, hands-on projects.
Vission:
To inspire and empower crafters of all experience levels to unlock their creative potential. Encourages hands-on experimentation, self-expression, and exploration through diverse craft projects.
Education:
- Bachelor of Arts (BA) in Craft and Material Studies – Virginia Commonwealth University.
- Specialized training in various crafting disciplines and material handling.
Recognition:
- Featured in local art exhibits for groundbreaking craft projects
- Partnered with community organizations to host crafting workshops
- Recognized for contributions to sustainable and eco-conscious crafting
Expertise:
Crafting expert with a focus on blending traditional techniques with innovative designs. Specialization:
- Textile arts (weaving, embroidery, fabric dyeing)
- Woodworking and furniture design
- Mixed media and upcycling projects