Satin fabric, renowned for its smooth texture and luxurious sheen, is popular for crafting elegant formal wear, stylish accessories, and sophisticated home décor items. However, the delicate nature of satin can make it a challenging material to handle. Its slippery surface and tendency to fray require careful preparation and precise techniques to achieve the desired results.
Understanding how to sew satin fabric is essential for creating flawless garments and projects, even for those with limited sewing experience. This article serves as a comprehensive guide to mastering the art of sewing satin, providing detailed steps, practical tips, and tricks to help you achieve a polished, professional finish. Whether you’re a beginner or an experienced sewer, learning the correct methods for working with satin will ensure your creations look stunning and hold up beautifully over time.
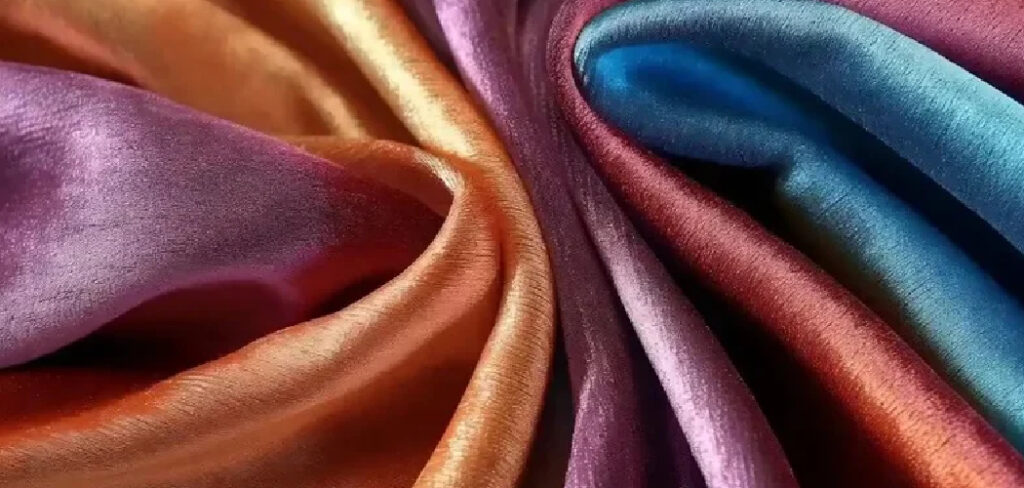
Understanding Satin Fabric
What is Satin?
Satin is not a fiber but a weave pattern characterized by its smooth, glossy surface on one side and a dull finish on the other. This weave can be created using various fibers, including silk, polyester, acetate, and nylon. The glossy appearance results from the weaving technique, where the threads are floated over several others before weaving under a thread, providing its signature sheen and texture.
Types of Satin
- Silk Satin: Known for its soft and luxurious feel, silk satin is one of the most elegant types of satin. However, it is delicate and requires extra care when handling and sewing.
- Polyester Satin: This type of satin is more durable and easier to sew than silk satin. Although it lacks the natural sheen of silk, it provides a more budget-friendly and user-friendly option for projects.
Challenges of Sewing Satin
- Slipperiness: Satin tends to shift and slide easily, making it challenging to keep fabric pieces aligned during sewing.
- Fraying: The edges of satin, especially silk satin, can unravel quickly, requiring careful handling and proper finishing techniques.
- Shiny Surface: Satin’s reflective surface can highlight imperfections, making precise stitching essential to avoid visible mistakes.
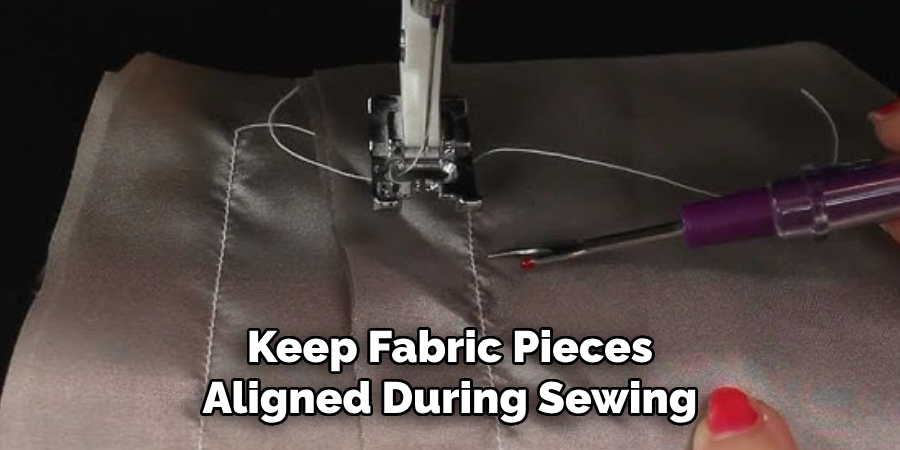
Materials and Tools Needed
Essential Materials
- Satin Fabric: Based on your project, choose the type of satin. Options include silk satin for a luxurious feel or synthetic satin for a more budget-friendly alternative.
- Matching Thread: Use silk thread for silk satin to maintain the fabric’s softness or polyester thread for synthetic satins to ensure strong, durable stitching.
- Lining Fabric (Optional): Adds structure and support, especially for garments or projects requiring additional stability.
Tools You’ll Need
- Sewing Machine: Opt for one with adjustable speed settings to maintain control while working with satin’s slippery texture.
- Fine Sewing Needle: Use a size 9 or 10 needle, as it creates smaller punctures, minimizing any risk of fabric damage.
- Pins or Fabric Clips: Avoid regular pins, which may leave permanent marks; instead, use alternative fastening methods like fabric clips.
- Scissors or Rotary Cutter: Essential for clean, accurate cuts to prevent fraying.
- Iron with Steam Function: A steam iron helps smooth the fabric, but must be used carefully to avoid burns or shine marks on the satin surface.
- Fabric Stabilizer (Optional): Provides additional structure, beneficial for intricate designs or detailed sewing projects.
Preparing Satin for Sewing
Step 1: Pre-Washing (if applicable)
Hand wash or machine wash satin fabric (depending on the fiber) to remove any excess dye or chemicals. Use a gentle detergent and cold water to prevent damage to the fabric’s delicate surface. Avoid using fabric softeners as they can affect satin’s texture and sheen. If drying is needed, air drying is recommended over tumble drying to preserve the fabric’s quality.
Step 2: Pressing the Fabric
Carefully iron the satin fabric before cutting to ensure it lies smooth and flat. Use a low heat setting on your iron, as high temperatures can scorch or damage the fabric. Always place a pressing cloth, such as a clean cotton sheet, between the iron and the satin to prevent shiny spots or burns. For best results, press on the wrong side of the fabric to avoid direct heat on the shiny surface.
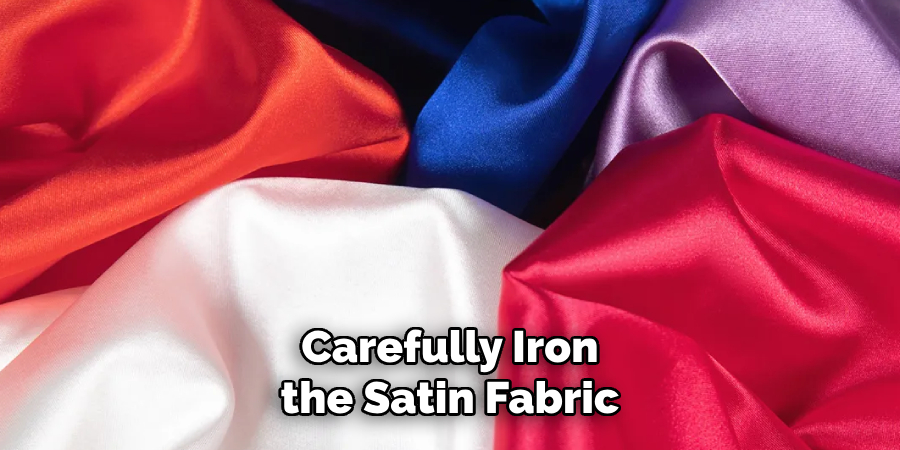
Step 3: Cutting the Fabric
Use sharp scissors or a rotary cutter to achieve clean and precise edges, as satin is prone to fraying. Cut the fabric slowly and deliberately to avoid mistakes, ensuring even cuts. Using a cutting mat with grid lines is advisable to help maintain accuracy. Adding pattern weights or clips will further secure the fabric as you cut.
Step 4: Using Fabric Stabilizer
Consider applying a fabric stabilizer if the satin feels too slippery or delicate during cutting or sewing. Lightweight interfacing can also help add structure to the fabric. These materials reduce slippage and make the satin easier to handle, especially for intricate designs or detailed sewing projects. Be sure to select stabilizers or interfacing appropriate for delicate fabrics to maintain satin’s softness and drape.
How to Sew Satin Fabric: Sewing Satin Fabric
Step 1: Adjusting Your Sewing Machine
Start by adjusting your sewing machine to accommodate this delicate fabric when sewing satin. Use a fine needle, such as size 9 or 10, specifically designed for lightweight or delicate materials to prevent snags or damage. Set your machine to a straight stitch or a small zigzag stitch if more flexibility is needed. Lower the sewing machine speed to control the fabric’s movement better, as satin tends to slip or shift easily under the presser foot.
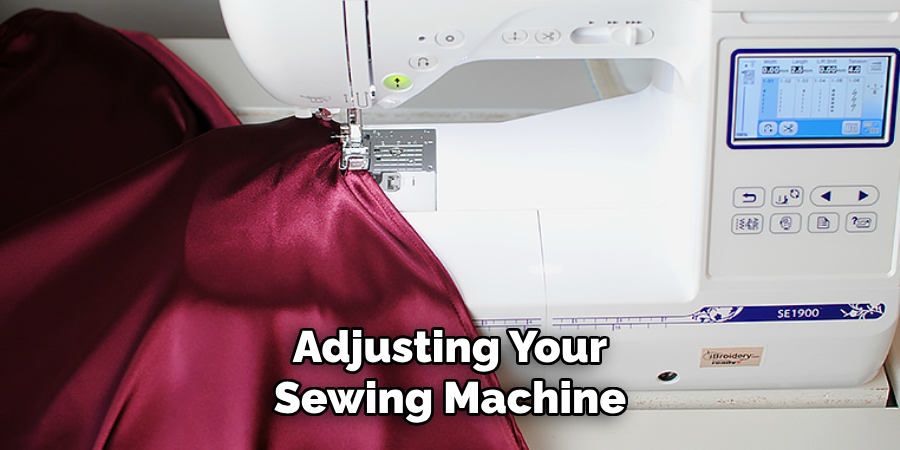
Step 2: Stitching Techniques
For clean and professional-looking seams, use a straight stitch with a short stitch length, typically between 1.5 and 2.5mm. This ensures tight, neat stitching that enhances the finish of your seams. If opting for a zigzag stitch, narrow the width to avoid leaving visible marks on the fabric. Sew at a steady, controlled pace to minimize the likelihood of the fabric bunching, shifting, or puckering during stitching.
Step 3: Pinning or Clipping the Fabric
Use fabric clips rather than pins to hold satin securely in place without leaving marks or holes. If pins are necessary, choose extra-fine ones made for delicate fabrics and handle them with care. Pin or clip as needed, ensuring the fabric edges are perfectly aligned to maintain precision and avoid uneven seams.
Step 4: Reinforcing Seams
Since satin is prone to fraying, it’s essential to properly finish the seams. Reinforce the seams using options such as a French seam, serged edges, or a narrow zigzag stitch. These techniques will protect the integrity of your finished project and keep it looking professional and durable over time.
Finishing the Edges
Step 1: French Seams
Ideal for silk satin, French seams provide a clean, professional finish by enclosing raw edges within the seam. To create a French seam, sew the fabric with the wrong sides together, using a narrow seam allowance. Trim the raw edges carefully to reduce bulk, then press the seam open. Next, fold the fabric with the right sides, encasing the trimmed edges. Sew along the edge to complete the seam, ensuring the raw edges are fully enclosed. This technique is perfect for lightweight satin, protecting the fabric while maintaining a polished appearance.
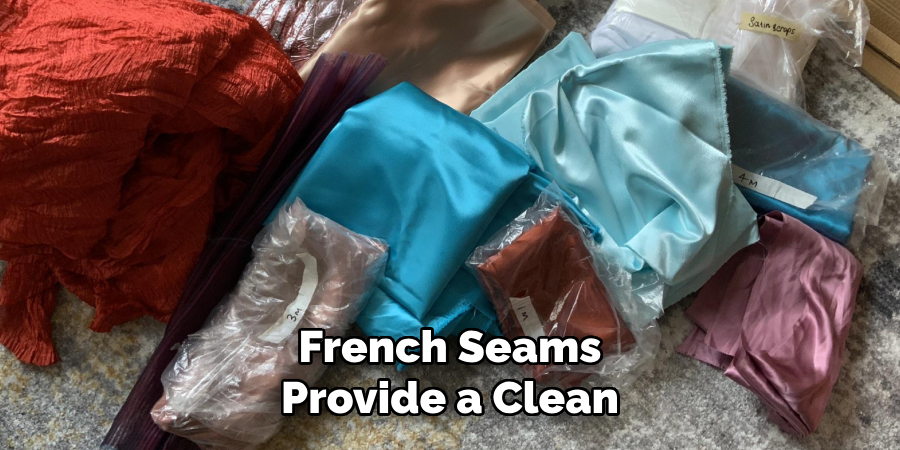
Step 2: Using a Serger or Overlock Stitch
For polyester satin or sturdier fabrics, using a serger or overlock stitch is an efficient way to finish the edges and prevent fraying. This method simultaneously trims the edge and applies a secure overlock stitch, saving time and providing a durable result. Adjust the settings on your serger to suit the fabric type, ensuring the tension and stitch width prevent puckering or stretching. This technique is particularly suitable for larger projects or garments that require consistent, clean finishes.
Step 3: Zigzag Stitching
For a simpler, more accessible method, a zigzag stitch can effectively prevent unraveling of the edges. Set your sewing machine to a zigzag stitch and adjust the stitch length and width to complement the satin fabric without compromising its sheen or texture. Carefully sew along the raw edges, ensuring that the stitches are evenly spaced for a neat finish. While this method is less intricate than French seams or serging, it offers a reliable and straightforward solution for satin projects.
Pressing and Final Touches
Step 1: Pressing the Seams
Always press satin seams gently with an iron on a low setting. Satin is a delicate fabric; high heat can scorch or damage it. To protect the fabric and avoid shine, use a pressing cloth between the iron and the satin. Avoid pressing directly on the satin, which can leave permanent marks or distort the fabric’s texture. Instead, work slowly and carefully to smooth the seams without applying excessive pressure.
Step 2: Adding Lining (Optional)
Consider adding a lining to your satin project for additional durability and comfort, and to prevent see-through issues. Choose a lightweight, breathable fabric that complements the satin’s drape. For a cohesive look, match the lining fabric to the outer satin or select a contrasting color to add a stylish flair. Attach the lining securely by sewing it to the edges or seams of the satin, taking care to prevent puckering or unevenness.
Step 3: Final Adjustments
Once the sewing is complete, review all seams for consistency and symmetry. Make any necessary adjustments to ensure everything lies flat and aligned. Trim any excess fabric and loose threads for a clean, polished finish. This final attention to detail will ensure your satin project looks professional and ready for use.
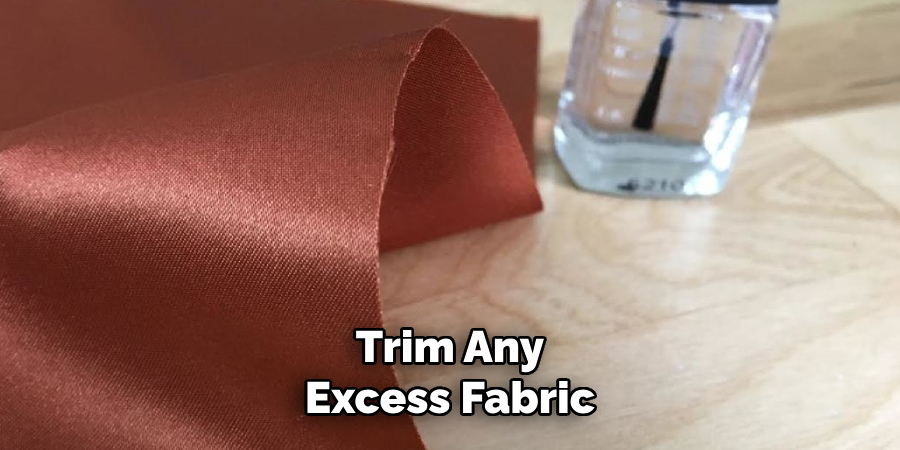
Troubleshooting Common Issues
Fabric Slipping or Shifting
Fabric slipping or shifting can be a common problem when working with satin. To address this, consider using a walking foot on your sewing machine, which helps feed the layers of fabric evenly. Alternatively, you can place tissue paper underneath the satin to stabilize it during the sewing process. This added layer prevents movement and ensures clean, precise stitching.
Shiny Marks or Pressing Marks
When exposed to heat, satin is prone to shiny marks or pressing marks. Always use a pressing cloth between the fabric and the iron to avoid this. The pressing cloth acts as a barrier, protecting the delicate satin surface from direct contact with heat while still providing enough warmth to smooth out wrinkles.
Seams Not Lining Up
Misaligned seams can detract from the overall look of your project. Prevent this by carefully pinning or using fabric clips to secure the fabric layers together. Sewing slowly also aids in maintaining better control over the fabric, ensuring that all seams align properly for a polished, professional finish.
Conclusion
Mastering how to sew satin fabric requires attention to detail and patience. By focusing on proper preparation, such as using the right needle, thread, and machine settings, you can ensure a smooth sewing experience. Careful stitching techniques, like sewing slowly and securing seams with pins or clips, help to maintain alignment and prevent mistakes. Proper finishing methods, such as using a pressing cloth to avoid damage, add a polished touch. Remember, practice makes perfect—experiment on scrap fabric to refine your skills. Take your time with satin projects to achieve professional results and showcase the true beauty of this delicate material.
Professional Focus:
Dedicated to exploring and advancing the intersection of traditional craftsmanship and contemporary design. Specializing in textile arts, woodworking, and mixed media, with a commitment to sustainable practices and the art of upcycling. Focused on creating meaningful connections through craft, empowering individuals to unlock their creativity, and preserving cultural heritage through innovative, hands-on projects.
Vission:
To inspire and empower crafters of all experience levels to unlock their creative potential. Encourages hands-on experimentation, self-expression, and exploration through diverse craft projects.
Education:
- Bachelor of Arts (BA) in Craft and Material Studies – Virginia Commonwealth University.
- Specialized training in various crafting disciplines and material handling.
Recognition:
- Featured in local art exhibits for groundbreaking craft projects
- Partnered with community organizations to host crafting workshops
- Recognized for contributions to sustainable and eco-conscious crafting
Expertise:
Crafting expert with a focus on blending traditional techniques with innovative designs. Specialization:
- Textile arts (weaving, embroidery, fabric dyeing)
- Woodworking and furniture design
- Mixed media and upcycling projects